In the electroplating of nickel 0.200 faraday – In the realm of electroplating, the precise deposition of nickel holds immense significance. The electroplating of nickel at 0.200 Faraday emerges as a crucial aspect, influencing the quality, properties, and applications of nickel coatings. This article delves into the fundamental principles, practical implications, and recent advancements associated with this specific charge density in nickel electroplating.
The electroplating process involves the transfer of metal ions from an electrolyte solution to a cathode surface, resulting in the formation of a metal coating. Nickel electroplating is widely employed in various industries due to its exceptional corrosion resistance, wear resistance, and aesthetic appeal.
The precise control of charge passed during electroplating, particularly at 0.200 Faraday, plays a vital role in determining the characteristics of the deposited nickel layer.
Electroplating Process Overview
Electroplating is an electrochemical process that involves the deposition of a metal coating onto a substrate by using an electric current. It plays a vital role in various industries, including automotive, aerospace, and electronics, for enhancing the properties of materials and improving their performance.
Nickel is a widely used metal in electroplating due to its exceptional properties, such as corrosion resistance, wear resistance, and magnetic properties. The electroplating process involves several steps, including surface preparation, electroplating bath preparation, and post-treatment.
Significance of 0.200 Faraday
Faraday’s constant is a fundamental constant in electrochemistry that represents the amount of charge required to deposit one mole of a substance. In the context of nickel electroplating, 0.200 Faraday is a significant value that corresponds to the deposition of one mole of nickel.
Understanding the significance of 0.200 Faraday is crucial for controlling the thickness and quality of the nickel coating. By adjusting the amount of charge passed through the electroplating bath, it is possible to precisely control the thickness of the deposited nickel layer.
Parameters Influencing Electroplating Quality
The quality of nickel electroplating is influenced by several key parameters, including:
- Current density: The current density affects the rate of deposition and the grain structure of the nickel coating.
- Bath temperature: The bath temperature influences the solubility of the nickel ions and the rate of diffusion.
- pH of the bath: The pH of the bath affects the stability of the electroplating solution and the morphology of the deposit.
By carefully controlling these parameters, it is possible to optimize the electroplating process and achieve high-quality nickel coatings.
Applications of Nickel Electroplating
Nickel electroplating finds applications in a wide range of industries and applications, including:
- Automotive: Nickel electroplating is used to provide corrosion protection and improve the wear resistance of automotive components.
- Aerospace: Nickel electroplating is used to protect aircraft components from corrosion and enhance their magnetic properties.
- Electronics: Nickel electroplating is used to provide electrical conductivity and corrosion protection in electronic components.
Nickel electroplating offers numerous advantages, such as improved corrosion resistance, enhanced wear resistance, increased electrical conductivity, and improved magnetic properties.
Recent Advancements in Nickel Electroplating, In the electroplating of nickel 0.200 faraday
Recent advancements in nickel electroplating technology have focused on improving the efficiency, quality, and sustainability of the process.
- Pulse plating: Pulse plating involves alternating the current between on and off periods, resulting in improved deposit quality and reduced porosity.
- Nanocomposite coatings: Nanocomposite coatings are formed by incorporating nanoparticles into the nickel electroplating bath, enhancing the properties of the deposit.
- Environmentally friendly electrolytes: Research is ongoing to develop more environmentally friendly electrolytes that reduce the use of hazardous chemicals.
These advancements are leading to the development of new applications and improved performance of nickel electroplated products.
Key Questions Answered: In The Electroplating Of Nickel 0.200 Faraday
What is the significance of 0.200 Faraday in nickel electroplating?
0.200 Faraday represents a specific amount of charge passed during electroplating, which influences the thickness, adhesion, and corrosion resistance of the deposited nickel layer.
How does charge passed affect the quality of nickel electroplating?
The amount of charge passed, including 0.200 Faraday, affects the thickness, grain structure, and other properties of the nickel coating, impacting its overall quality and performance.
What are the applications of nickel electroplating?
Nickel electroplating finds applications in automotive, electronics, aerospace, and other industries, providing corrosion protection, wear resistance, and enhanced aesthetics.
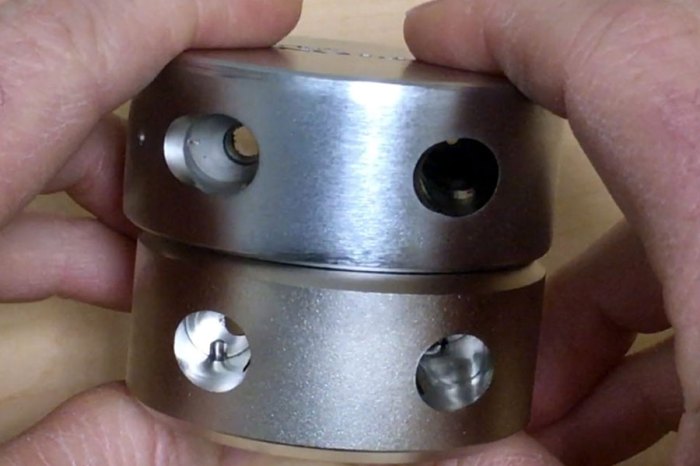
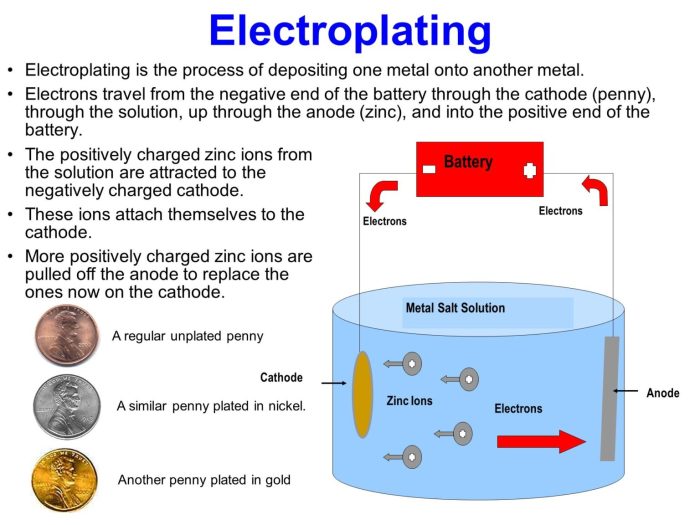